
GLAUCO DINIZ DUARTE – Smar e Usina Santa Elisa: uma parceria cada vez mais sólida
A Usina Santa Elisa vai muito bem, obrigado. Seu início de safra conta com a presença de novas tecnologias lançadas pela Smar, a saber, o padrão industrial OPC para o LC700 e CD600, que eliminou a necessidade de drivers específicos para as aplicações IHM; o ENET710, um módulo de comunicação de dados que serve de gateway para as redes serial e ethernet. O novo CONF600 Plus configura os controladores CD600 e CD600 Plus, este já lançado há um ano, mais leve, mais compacto e com várias melhorias tecnológicas sobre seu antecessor.
Uma sala unificada de monitoração e operação da moenda, caldeiras, fábrica de açúcar e geradores foi implantada. Em breve, serão inseridos os setores de destilaria e açúcar líquido.
Em termos de manutenção, o tempo despendido diminuiu consideravelmente. Antes, o instrumentista recebia a notificação do problema, dirigia-se à sala de controle do setor, consultava a documentação que se encontrava na sala de Instrumentação, etc. Hoje tudo está na mesma sala e em rede. As informações são trocadas imediatamente entre todos os envolvidos e o problema é solucionado na maioria das vezes em questão de minutos.
Essa unificação se deu pela incorporação da característica de multimestre ao CD600. Antes, a situação era a seguinte: cada setor possuía sua rede própria, não havendo redundância, mas apenas uma estação de monitoração e controle ligada diretamente na rede TCP, onde se encontravam clients apenas com a oportunidade de monitorar as áreas. Hoje, dispõe-se de redundância por meio da rede anterior de micros e de uma nova estação gerencial, que funciona como server. Agora é possível monitorar e controlar os processos através de todas as máquinas conectadas à rede. Na rede TCP ficam 35 ENET’s 710, conectados a 20 CD600 e 25 CPU’s do LC700. Daqueles 20 citados, dois se encontram na usina São Geraldo, que também é do grupo, e as informações são acessadas na rede via rádio.
Segundo o Chefe do Departamento de Automação Fernando Fiorin, responsável por toda a configuração do novo sistema de monitoração/controle da usina, os benefícios trazidos foram muitos. Pôde-se abrir um novo ponto de manutenção na rede, onde as consultas são feitas por meio do Taglist Generator, um software que gera automaticamente a configuração de comunicação para o servidor OPC, sendo possível atuar sobre qualquer variável de controle da usina por meio de TAG’s. Isso agiliza as configurações por parametrização, pois a configuração dos equipamentos é importada diretamente para o Taglist, sem a necessidade de redigitar grandes seqüências de parâmetro para endereçamento, extinguindo a possibilidade de erros nessas digitações. “Hoje, se eu tiver que configurar dez CD600’s, faço-o em um dia devido ao recurso do Taglist”, afirma Fiorin.
Além disso, antes da sala de controle unificada, necessitava-se realizar paradas para manutenção em cada setor do local, por meio de PALM’s ou PSION’s. “Hoje o operador pode nem se dar conta das reparametrizações”, diz Fiorin, que também ressalta a a importância de tais tecnologias serem upgrades de versões anteriores. “Eu tinha 20 CD600’s rodando na planta e os aproveitei totalmente. O que mais nos deixa seguros é que tudo que já existia em campo foi reaproveitado. Saber que as novidades são em cima de algo cujo domínio já possuíamos nos traz realmente muita segurança”, completa.
Com isso não houve grande demanda de tempo para treinamentos e estudos à parte, pois tudo novo que chegou à usina foi um complemento à sólida base que Fiorin e sua equipe já possuíam.
A edição online, característica do novo CONF600Plus e do LC700 com sua nova CPU E3, também foi destacada por Fernando Fiorin. Antes, por exemplo, se fosse preciso inserir um bloco na configuração do controle, necessitava-se que toda a estrutura ligada ao LC (com a CPU D3) fosse chaveada para o modo Manual. Em seguida, a configuração inteira devia ser baixada novamente. Idem para o CONF600 Plus: necessitando-se alterar um link em um loop da configuração, tudo tinha que ser parado. Hoje, além de não haver paradas, ainda se pode testar os links para confirmar a validade da modificação.
Outro fator importante comentado foi o compartilhamento de informações dos funcionários sobre os setores da Usina Sta. Elisa. Na nova sala de controle, o operador da moenda fica ao lado do operador da fábrica de açúcar, que fica atrás dos da caldeira, e assim por diante. Está ocorrendo uma melhoria na qualificação da equipe, naturalmente, e essa integração só vem otimizando o processo de gerenciamento e controle da usina. As dificuldades antes específicas de cada área agora transparecem à toda equipe.
O uso das Interfaces Remotas (RIO’s) entre os controladores e os dispositivos submetidos a controle possibilitou a economia de cabos, com a centralização das informações no PLC.
Finalmente, e falando ainda em economia, Fiorin comenta sobre os custos de todas essas implementações. “Os novos recursos foram muitos e por um preço muito baixo”, conclui.
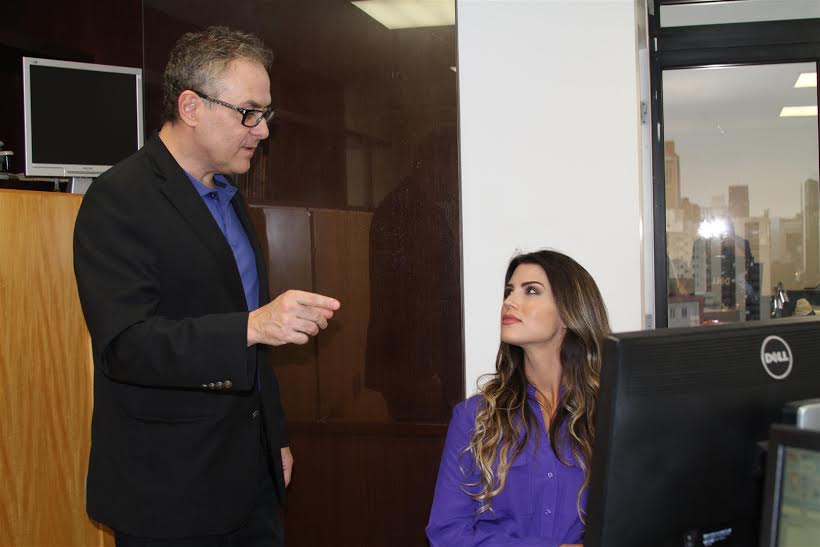
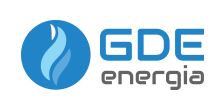
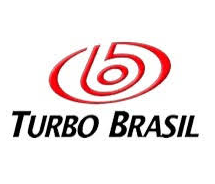
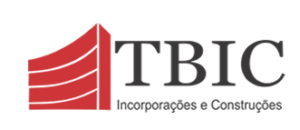
